August 15, 2018
Twenty-one days to find out if we have poisoned our members. We wait charily as the results we’re expecting could potentially bring this place to its knees; if the independent Air quality test of our pilot studio in Hoxton turns out toxic, then we’ve failed five years of endeavour and hard work.
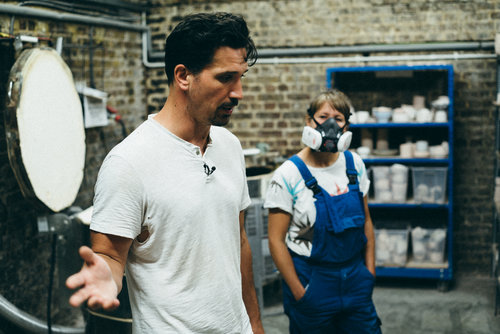
When we first started out we just didn’t know what was what, or even how to find out. Clay dust: Bad, that’s about all we had. Opening a studio, we knew it had to be kept clean, but how clean and how would you know if you were getting it right?
It’s a costly and voluntary procedure but we knew it had to be done. We called a company called Euro-Environmental in May this year, who came and positioned mini air-sample devices that looked like spy-gadgets onto our team’s aprons, onto our members’ clothes and in potential hotspots all over the studio. Then they came back eight hours later and took them for analysis.
Lungs, they are extraordinarily valuable bits of kit, and somewhat fragile. As an ex-respiratory nurse in a ceramics studio these vital organs at once became a constant cause of arresting consideration for me. Having seen the very real and sobering, untreatable effects of lung cancer, emphysema and other devastating chest conditions, managing and maintaining a healthy studio safe enough for some 300 members of the public a week has felt like a dust-crusted Sword of Damocles.
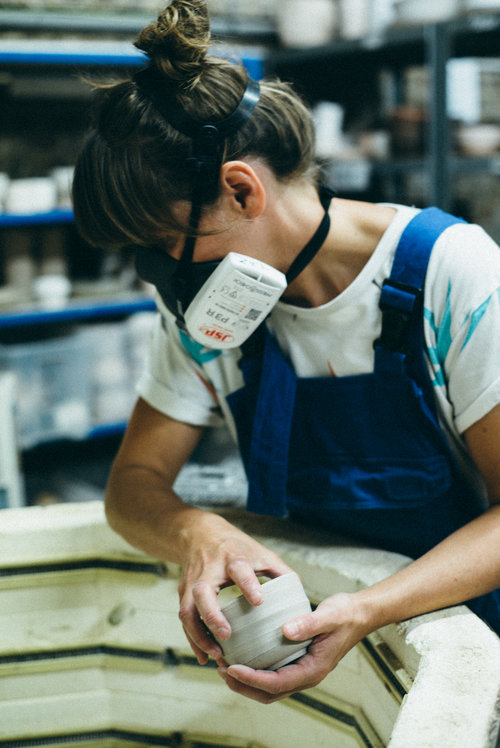
Silica, its whole inevitable existence can potentially take all the fun out of clay; and all the oxygen from your airways, forever. It is a pernicious substance, even in small doses, once it enters the lungs it dwells there and stubbornly denies your lymph system any recourse to dispatch it; gradually taking over and slowly suffocating you. The studio, it turned out, rather disturbingly, is full of robust sources of this substance. Kilns for example, merrily pump out the stuff all night long (as well as thousands of other toxins). Therefore for the sake of the public and our team, we realised all systems needed to be carefully designed and constantly updated to minimise the breathable levels of silica dust in the air.
So we got venting and mopping, staff, mentors and members all, we sent out grave reminders in our newsletter to the whole of the membership: Clean up after yourselves, for the love of breathable air! Every nook seemed to be a source of clay crumbs and dust. In fact, anywhere anybody did anything would immediately generate a mountain of dust.
I get some good news: I find out that something called a P3 respirator can protect you from breathing in Silica. They’re not cheap but I buy a load plus spares for all the staff and make them wear them when cleaning, and then I decided while loading kilns, and then when consolidating shelves. Not to mention mixing glazes. I just didn’t know. Should we insist the whole membership wear them?
Our mantra is now: It’s not the person; it’s the system. Although, people operate the system of course. So, as well as attempting to instill a sense of ownership and responsibility into the mindset of the membership via the newsletter and handbook, (terrifying them with tales of the effects of silicosis and issuing constant reminders of the necessity for good cleaning practices; also segueing clauses for cleaning times into their contracts) we have had to slowly build in operational systems into our rota to prevent unknowable chaos getting the better of us. Each change to the procedure has slightly upgraded the last.
This is by no means a simple undertaking and it is credit to our unflappable staff who carry out the heavy work to protect us all every day. The processes are always subject to upgrade - in fact ‘All systems can be improved’ is another of our favourite maxims - because you have to make them work as efficiently as possible. Minimal input for maximum output with zero waste: That’s the dream.
But has it actually meant anything at all? Has it made a difference after all this shifting and mopping and wet-vacuuming and rotas, respirators, sweat and haranguing people ? Or has it been moving furniture on the Titanic?
The results come in via email and I scroll through all the preamble. Hands shaking.
Respirable Crystaline Silica: 0.028mgs/m3 In all areas, <35% WEL
What does that mean?
Status Workplace Exposure Limit: Insignificant!
Insignificant! in all areas of testing.
I want to hug the team.
Lewis Maughan
Turning Earth Operational Manager
March 12, 2018
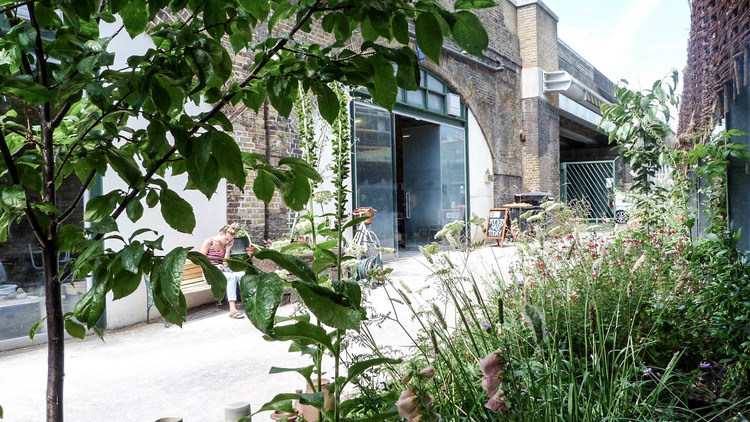
Turning Earth / Make Space Conference
A peer-to-peer learning opportunity
How do you create a ceramics makerspace?
Thurs 10 / Fri 11 / Sat 12 May 2018
Turning Earth believes that if hand making were a widespread way of life, we’d all be better off. This belief is at the heart of everything we do.
We think makerspaces can help replace unsustainable consumerism with a kinder, more fulfilling approach to life. We want to see this movement make rapid progress, renewing communities in each corner of the world through the creation of new meeting places. We believe that makerspaces are the thriving community centres of tomorrow.
Since Turning Earth opened in 2013, a large number of people have approached us for advice about how to set up a similar space in their area. In some cases we have received more than one approach from people living in the same city who weren’t aware of each other. We want to create a focused, efficient way to share our knowledge and answer questions that other entrepreneurs have in depth. We also want to learn from the experience of others and create a platform for new partnerships and friendships.
Makerspaces are creating empowering new models for peer-to-peer learning between makers. Now we'd like to extend this philosophy to the makers of makerspaces.
SOLD OUT
The conference is available to anyone anywhere, whether their project is still in development or already up and running. It will benefit entrepreneurs in both urban and rural settings, whether they have ceramics knowledge, or a business background, or neither, or both. Visionaries across the UK and Europe and further afield are working separately for the same purpose, many with mutually beneficial skill sets. We think we would all gain enormously from the opportunity to come together with others.
In addition to the syllabus outlined below, there will be opportunities to share experience and to ask questions both of Turning Earth’s directors, and of each other. In this short two day intensive we will cover a lot of ground and connect in a way that empowers us all to form lasting working relationships and friendships.
Participants will leave the event plugged in to an independent ‘Make Space for Ceramics’ network, with a private Facebook group for continued knowledge sharing after the event, alongside any other coordinated activities decided by the group.
This event is entirely non-profit: all the money taken will be used to cover the costs of the event. A limited number of half price early bird tickets are available and additional people from the same team can come at a reduced cost.
Please note, as we have a number of projects in development in London, we request that you contact us separately before signing up if you would like to open up in this city. We are currently developing some exciting local partnership and franchise opportunities, and we want to be careful to ensure that we work with local entrepreneurs in a collaborative and mutually empowering way.
Schedule
Meet & Greet at Turning Earth E2: Thursday 10th May, 6.30pm
Conference at Hoxton Hall E2: Friday and Saturday 11th and 12th May, 10-6 pm
Turning Earth E10 tour and social Friday evening
Prices
Early bird - £60
Regular price - £120
Additional team members - £40
Topics include: Business modelling, Financing, Finding sites, Marketing and brand, Operations and systems, Classes and membership, Member management, Human resources, Accountancy and legal, Equipment, Leadership, Collaboration
Participants include:
Lewis Maughan, MD Turning Earth
Tallie Maughan, Founder Turning Earth
James Otter, MD Potclays
UK Crafts Council
Syllabus
1. Business model creation
What makes a good location
Working from vision
Limitation as a creative tool
2. Site and operations
Power
Water
Waste
Air quality and ventilation
Air temperature
Security
Fire and health and safety
Risk assessments and compliance
3. Sourcing equipment
Suppliers
Points to consider
Q&A with James Otter, MD of Potclays
4. Marketing and brand
Developing your brand
An integrated approach
Interior design: aesthetics and functionality
Online community building
Social media platforms
Visual imagery
Events
Data mining and contact lists
5. Classes and memberships
Course content
Selling courses
The importance of open-access/membership
How to integrate open-access/membership
6. Membership management
Back end systems
Customising online management systems
Onboarding and exits
Managing expectations
Training your usergroup
Trust-based models
Managing security
7. Systems and processes
Management through limitation
Buying and selling materials
Cleaning
Glazing
Waste clay and reclaim
Firing
8. Human resources
Building your team
Handling the skills shortage
Training
Contracts
Financial considerations
9. Accountancy and legal
Bookkeeping
Streamlining using apps
Formation of your company/organisation
Ownership
Forms of social enterprise
Rental issues
10. Leadership
Healthy communities
The role of vision and values
Inclusion
Dealing with challenges
Complaints
Community outreach
11. Financing
Funding sources
The 'art in the black' profit model
Business planning and financial forecasting
Estimating costs
Lean start-up model
12. Collaboration
Peer support
Turning Earth resources
Makerspaces as a collaborative model
Towards a common vision
13. Resources